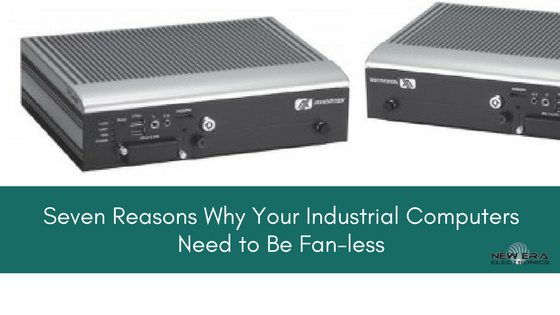
Seven Reasons Why Your Industrial Computers Need to Be Fanless
Blog
If you work in heavy industry, mining, manufacturing, the military, transportation, even healthcare, you know that conventional computers are not robust enough to withstand harsh industrial environments and can sometimes spread debris and contaminants. Conventional computers have fans to cool parts and components. These fans bothdraw in hot and dusty air and blow air out (and debris with it). One waygreatly affects a computer’s performance; the other can adversely affect other things nearby.
Whereas the traditional computer is usually set up in an air conditioned office or isolated space, devices used in industry often have to contend with extreme temperatures,dirty environments, even shock and harsh lighting. They have to be built rugged to handle punishment.
Eliminate these problems for your workplace and demands. Get the latest fanless industrial computersand reap the benefits.
Thermal Design
Look carefully when you choose equipment that is promoted as “fanless”. Poorly marketed models may have no fans for the processors and motherboards, but still have fans elsewhere insidethe chassis for cooling nonetheless. An industrial computer with good thermal design will be truly fanless. It will dissipate heat more efficiently and operate comfortably in much wider temperature variations.
Fanless should mean what it says. That means an industrial computerhas no cooling fans anywhere. It uses chassis heatsinks and internal piping instead.
It’s Easy to Become a Fan of Fanless
Quite simply, fanless industrial computers kick butt, especially in plant automation, process control, and ‘smart factory’ situations.
- Passive Heat Sink = No Moving Parts.Get a passive heat sink to repel heat because it truly is fanless. (Active heat sinks have fans.) The CPU needs cooling and a passive heat sink sits atop the CPU to divert heat away and out using fins.
- No Debris.Many computer fans blow inward, sucking in cooler air but also dust, dirt and many other things. This debris builds up, affects performance, and can lead to computer failure.
- Greater reliability. Fans are one of the biggest causes of failure in conventional computer hardware. If the fan fails, other problems are sometimes minutes away as heat builds up. You want better reliability and have improved Mean Time Between Failure (MTBF).
- Energy efficiency. Heat sinks are far more energy efficient than fans. Conserving energy reduces cost and impact on the environment. Power is often at a premium and margins are tight in today’s market.
- Location Flexibility. Fanless computers can go where computers with fans can’t handle the conditions. For example, near moisture or even outside. Or how about in an operating room? Medical computers need to be fanless to ensure no contaminants are spread around in the sterile OR.
- Form factor flexibility. Small spaces are a big consideration when designing equipment for industrial applications. Some fanless systems can be designed smaller. Smaller form factor means better options for situating industrial computers. This is a major cost benefit, but also an advantage in situations where equipment is hard to reach. Not only do you get longer life out of your computers, you cut maintenance costs.
- Eliminate moving parts. As mentioned, a fan is one of the components of a computer that is most likely to fail. It is also sensitive to shock and vibration conditions that are hard to eliminate in an industrial environment. By eliminating fans, you extend computer life and reduce maintenance costs.
If you need advice about selecting equipment, a no-obligation consultation with helpful partners is a simple phone call or email away.
Brian Luckman is the President of New Era Electronics. He has worked in the industrial OEM market for over 25 years, serving a variety of different industries, gaining a strong reputation for his expertise and a thorough understanding of how to properly service OEM customers. In 2000 he began New Era Electronics and the company continues to grow. He’s a husband and father and enjoys exploring the outdoors.
Creative Commons Attribution: Permission is granted to repost this article in its entirety with credit to New Era Electronics and a clickable link back to this page.